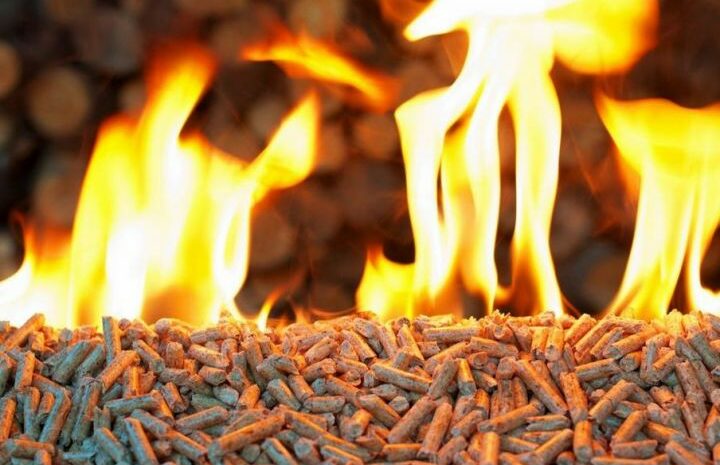
Mistakes and risks of switching to alternative fuels – say elevators
What are the mistakes and risks of switching to alternative fuels?
The transition of the elevator to alternative fuels is not ideal. Practitioners talked about the problems they encountered when using the elevator alternative, the difficulties that may arise, and how to deal with it all. The experience was shared at the forum “Own Elevator”.
Selection and installation of a heat generator
The first thing that Mykola Bevz, Deputy Director for Grain Storage and Processing of the Western Bug Company, draws the attention of colleagues is the correct selection of the heat generator capacity and its location on the territory. An error with the location of the generator relative to the grain dryer can “eat” up to 25% of the drying power.
According to the head, the elevators have a task to save fuel, so the Sokal Elevator of the Western Bug company last season switched the Bonfanti grain dryer to an alternative fuel – sunflower husk pellets.
“If you look at corn, we wanted to take an additional 700 tons of corn and remove about 10 tons * of moisture from the grain. In fact, in view of this, a solid fuel boiler was urgently installed, because it became clear what the market situation will be with gas. The gas burner was preserved, “Mykola Bevz said.
According to the head, an 8 MW heat generator was installed on the new Bonfanti 8000 grain dryer. However, after the launch, it became clear that the dryer does not “extract” the necessary operating parameters at this capacity of the boiler, and the company almost immediately put a stronger boiler at 9 MW.
“As soon as we replaced the boiler with a more powerful one, the situation changed immediately, in fact the boiler started working normally. The lining in the heat generator stopped collapsing, we stopped making frequent stops, ”says Mykola Bevz.
The head draws attention to the fact that when selecting heat generators for elevators, as a rule, there are no technicians of a high enough level who could analyze and check the correct choice of equipment capacity. But it is at the stage of selection that the feasibility study of the heat generator capacity is important. It is necessary to understand whether the calculations made for further work are really justified, and whether it is worth investing in equipment.
Fuel whips of different materials. Photo illustrative
The next important point is the selection of a place for the heat generator relative to the grain dryer. According to Mykola Bevza, due to the peculiarities of the existing equipment, the heat generator was not very successfully installed on the elevator, as the heat hoses from the boiler go to the grain dryer not in a straight line, but with a turn. As it turned out, such angles on the path of the heat agent to the dryer take up to 20-25% of its efficiency.
The manager says that due to these factors, the grain dryer cannot reach 100% capacity and uses more fuel than necessary.
According to Mykola Bevza, the capacity of the grain dryer on alternative fuel can correspond to the declared by the manufacturer only if the dryer is designed for biofuels. Dryers that are designed to run on natural gas and have recovery, lose up to 30% of productivity. At the Western Bug elevator, they hope to renovate or buy another dryer without recuperation next year to compare grain drying performance against this factor.
Also interesting: Energy crisis – how energy prices have affected elevators, equipment manufacturers and flour mills
Fuel optimization – movable floor
The heat generator must ensure an uninterrupted supply of fuel: either to attract additional human resources, or to automate the supply without the involvement of workers. At the elevator of Agrotekhnika LLC in the village of Charukiv in Volyn followed the path of automation.
Elevator LLC “Agrotechnics” in the village. Charukiv in Volyn
According to Andriy Hlubitskyi, head of the elevator farm at Agrotechnika LLC, alternative fuel has been used at the elevator since the start of the plant, as the gas infrastructure is too far away. Initially, straw was used as fuel, and in 2019 a Bonfanti dryer and a 6 MW heat generator were installed in the elevator. The equipment was set on the condition that the grain dryer will work on wood chips – technological chips, which are manufactured in a group of companies. Fuel supply was automated.
“In order not to attract many people for the uninterrupted supply of chips in the elevator built a so-called movable floor. With its help the chip is automatically fed into the heat generator. No extra labor required. In case of insufficient amount of technological chips in the hopper, the movable floor is automatically switched on, and chips are fed to the receiving hopper by conveyors, and from there – by the same mechanism to the heat generator, ”Andriy Hlubitsky said.
According to the specialist, the conveyor of the movable floor consists of two parts: one lifts the chips from the pit with a volume of 90 cubic meters, where the fuel is stored, the other delivers it to the receiving hopper.
According to Andriy Hlubitsky, the technology of the movable floor is effective, but there are nuances in working with wood chips. The chips fraction is not always stable, and large pieces of wood can jam the screws in the receiving hopper. Then less fuel is fed into the heat generator and the temperature drops. Therefore, the operator’s task is to always pay attention to this aspect of work.
Wood chips, wood chips – a popular alternative fuel. Photo illustrative
This year, pine chips are used at the Agrotekhnika elevator. The material has good flowability, but it also depends on humidity.
“The fraction is about 25-35 mm, it is very convenient and the chips do not get stuck in the screws and wake up well. If the pine is dry – it’s easier, then the flowability is much better. If the wood chips are wet, it starts to “hang”, respectively, empty holes are formed in the receiving hopper, the temperature in the boiler drops, “says Andriy Hlubitsky.
According to the head, during the three seasons of drying corn in the elevator and failed to bring the grain dryer to the required performance indicators, the equipment works on 2/3 of its efficiency. To reduce the impact of the human factor on the operation of the heat generator, namely – maintaining a stable temperature – the elevator plans to improve the system: install a sound signal that would respond to temperature drops. This will quickly affect the productivity of the grain dryer.
At the Western Bug elevator, they also want to improve the process of controlling pellet costs. The idea is to put strain gauges in the receiving hopper, which determine the fuel level and signal the need for it. As Mykola Bevz noted, such an improvement is very necessary, because the pellet warehouse is far from the heat generator, and fuel delivery takes some time.
Nuances of work with wood chips and pellets
At the Agrotekhnika elevator they experimented with different types of solid fuels: they used sunflower, pine and energy willow pellets.
According to Andriy Hlubitsky, sunflower pellets have proven themselves well due to the stability of combustion. But pine pellets “skidded” the work: the expert says that such fuel should be used to clean the heat generator very often due to the high ash content of the material.
“We tried to dry the grain on the energy willow this year. There is a willow that grows very quickly. It is also quite effective. Plus it is that the wood chips are dry and very loose. Minus – it is thin, because it is a soft tree species, it burns very quickly. The experiment showed that 3 kg of energy willow is used to remove 1 t /% of moisture from corn. For comparison: pine chips need 2.5 kg per 1 t /% of moisture, ”Andriy Hlubitsky said.
Chips from energy willow. Photo: Kurkul.com
Another important point: any fuel has suppliers, and they also affect the stability of the elevator. Without a reliable supplier, ready to bring pellets or wood chips to the elevator at any time of the day, uninterrupted drying of grain will not work.
Warning: fire hazard
After installing the heat generator on the elevator, it is necessary to take care of comprehensive training of personnel, Mykola Bevz emphasizes. Training should be provided by equipment suppliers, and it should apply to each stage of the work: how the dryer is tied to the technological process, how it should work with the heat generator, what are the emergency modes, etc.
Example from practice: there may be a situation when the receiving hopper of the generator is clogged with a hole through which the fuel enters the boiler. This increases the risk of fire.
“A slide is formed in the hole like magma, and the pellet no longer falls asleep in the boiler. In this case, there may be throwing charred pieces or sparks in the opposite direction, and then the wind “twists” them near the boiler. That is why it is important that the staff is always informed, instructed, and disciplined in terms of their work, ”says Mykola Bevz.
Despite all the difficulties faced by elevators, the benefits of an alternative to a granary are obvious: independence from the price and availability of natural gas. Thus, using wood chips in the elevator of Agrotechnika LLC, the cost of removing 1 t /% of corn moisture is about 30% less than on pellets.
Therefore, we summarize everything that practices recommend for quality drying of grain on alternative fuels:
make sure of the correct choice of boiler power and its proper placement in the elevator,
automate the supply of fuel to the heat generator,
find a reliable fuel supplier
when working with pellets, minimize the number of loads and unloadings of fuel, so as not to disrupt the structure of the pellets,
pay due attention to staff training,
minimize the risk of fire due to the operation of the heat generator.
Source https://elevatorist.com/blog/read/758-pomilki-i-riziki-pri-perehodi-na-alternativne-palivo–rozpovidayut-elevatoristi?fbclid=IwAR0djOsPvqMy5AcBZg-RKEK0q3EtZkBBF